Advantages of adhesive stacking technique
- Enhanced geometrical and electromagnetic properties
- Reduced electrical losses
- Reduction of eddy currents
- Integration in punching process possible
- Increased motor efficiency due to higher stacking factor
Customer Benefits
- Freely accessible technology for every producer of laminated cores - easy in-house realisation
- Low investment due to possible integration of adhesive application unit into already existing production lines
- Adhesive stacking technique meets the increasing requirements for the production of high-efficiency motors versus commonly used technologies
- Increase of motor efficiency up to 3 %
- Reduced scrap rate due to reliable part quality
Process description
- In line, a sufficient number of tiny adhesive drops is applied to the coated steel strip.
- Metal strip feeding to the blanking punch.
- The metal laminations are punched out.
- The growing stack is held by a choke system and passes through a moderately heated area.
- After a short period of time the complete stack leaves the tool sufficiently bonded.
Engineered by BAUER Lean-Engineering GmbH
Adhesive properties
The low to medium viscosity products 2206 and 2124 are specially developed for reliable bonding of electrically insulated stator or rotor laminations into stacks. They are easy to dispense automatically. Curing can take place in a short time by increasing the temperature during the stamping process. 2124 can also be used in combination with the special solvent-based activators 2900 or 2901 to achieve fast curing at room temperature. The self-levelling, capillary flowing 2206 can only be cured thermally (≥ 100°C). Both adhesives lead to high-strength, slightly tough-elastic bonds that are also resistant to hot ATF oils.
Specifications
Characteristics | Condition |
---|---|
Product category | Modified Urethanacrylate |
Color | Light yellow |
Viscosity [mPas] | 300 - 500 |
Tensile shear strength [N/mm2] (Steel-Steel; DIN EN 1465) | >13 |
Compression shear strength [N/mm2] (DIN EN ISO 10123) | >21 |
Temperature range [°C] | -55 – +175 |
Specifications
Characteristics | Condition |
---|---|
Product category | Modified Urethanacrylate |
Color | Light yellow |
Viscosity [mPas] | 55 - 85 |
Tensile shear strength [N/mm2] (Steel-Steel; DIN EN 1465) | >13 |
Compression shear strength [N/mm2] (DIN EN ISO 10123) | >21 |
Temperature range [°C] | -55 – +175 |
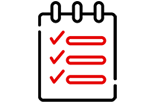
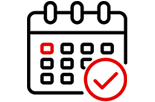
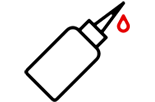
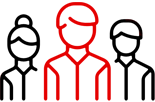
This is where you can get your individual offer or your personal sample.
You can also schedule an appointment with us or contact one of our application specialists.
Click here to get in contact with us